CATEGORIES
FEATURED PRODUCTS
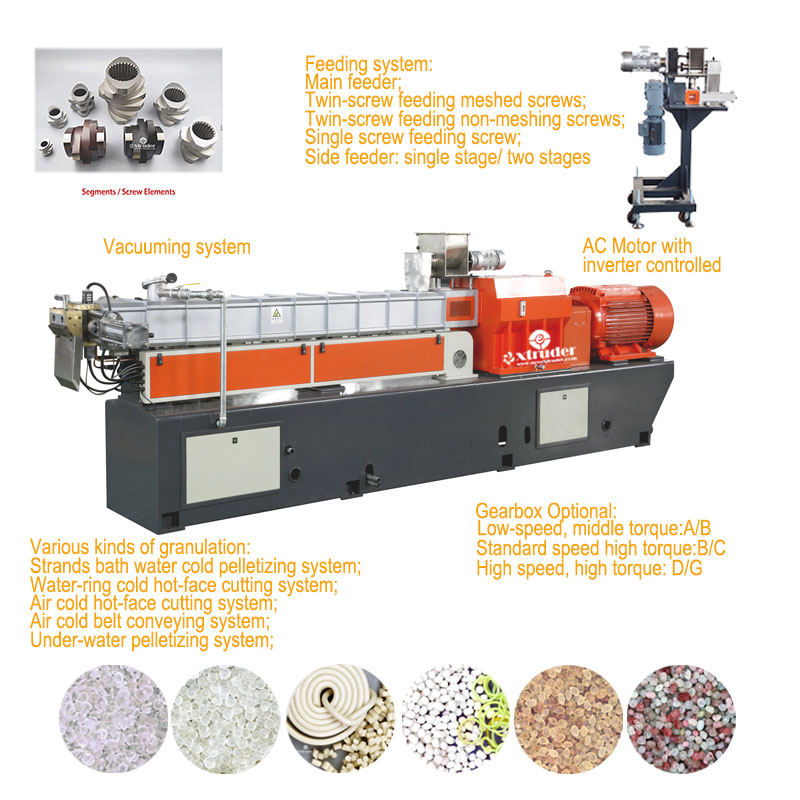
SHJ Series of Plastic modification Twin-screw extruder
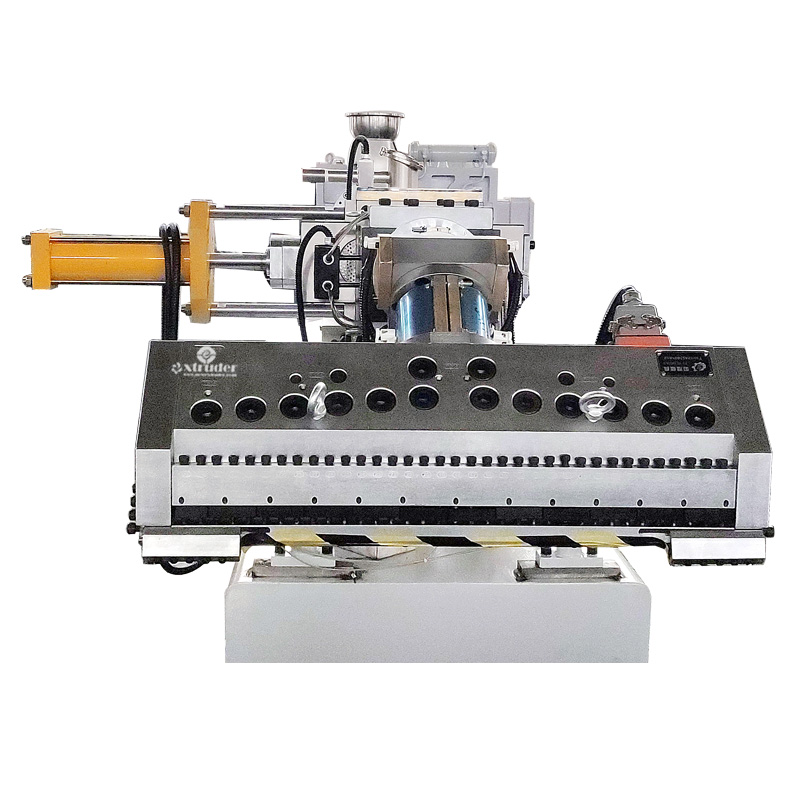
Plastic Sheets Extruder PE PP PVC PBS PLA Sheets Machine Lines
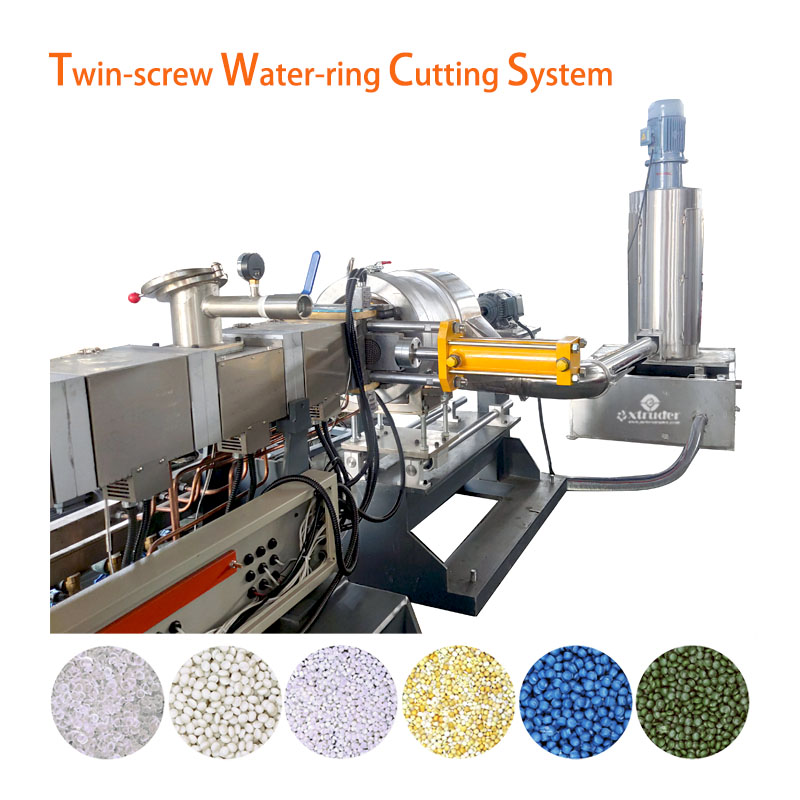
WATER-RING PELLETIZING SYSTEM TWIN SCREW PLASTIC POE EXTRUDER
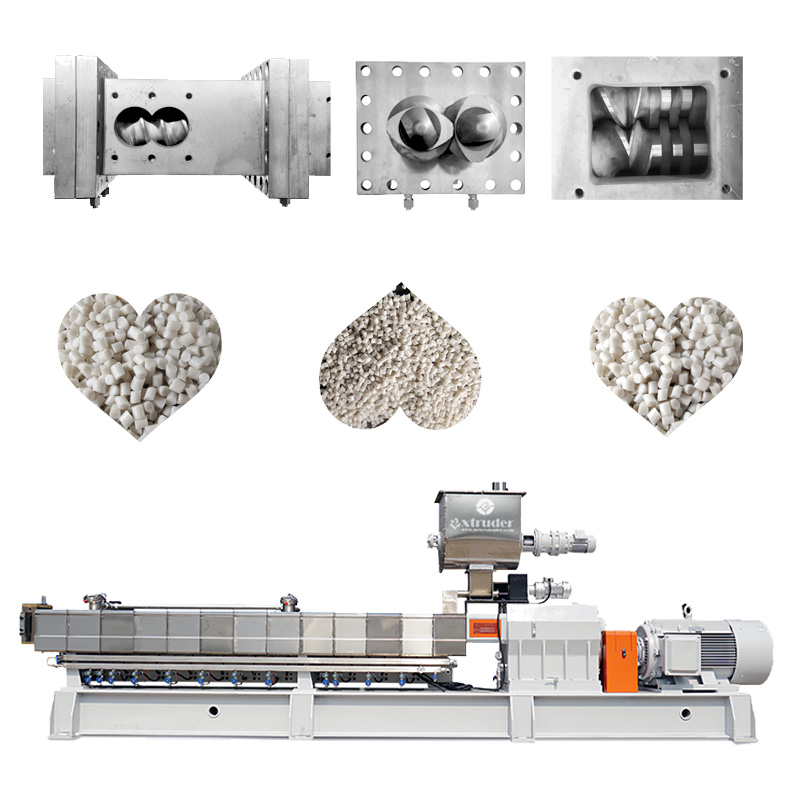
EVA Titanium powder added Photovoltaic PV membrane granules extruder large output capacity plasitc extruder
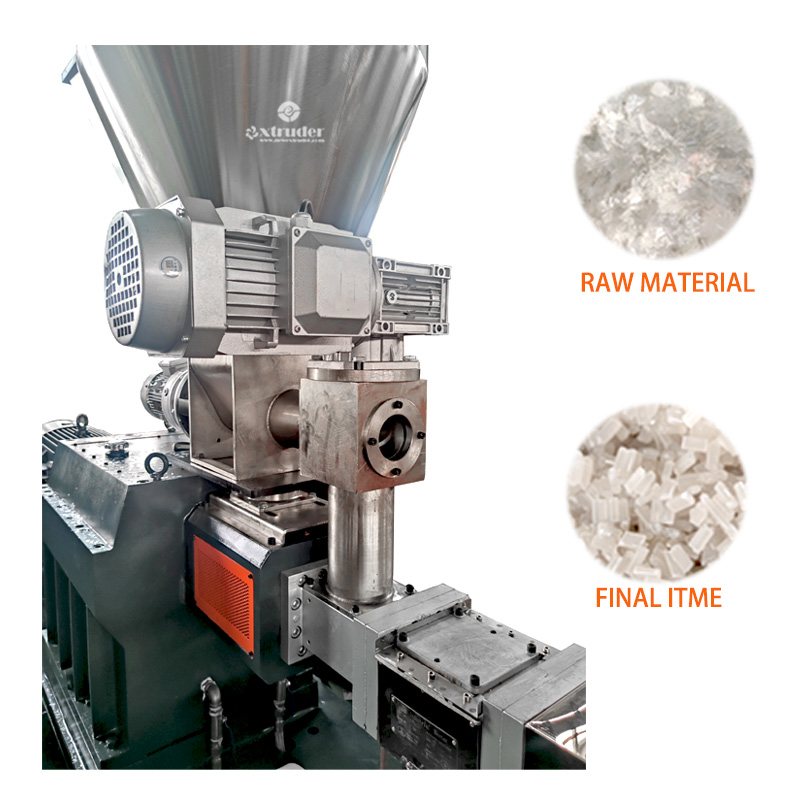
Recycling plastic regranulation extruder machine PE PP PET ABS recover granulation system recycling and reusing extruder
Color Masterbatch Extruder High Filling Calcium Carbonate Powder Twinscrew Plastic Extruder
SHORT DESCRIPTION:
Color Masterbatch Extruder High Filling Calcium Carbonate Powder Twinscrew Plastic Extruder
- Product Detail
- Our machine can process the following materials:
- Product Tags
Color Masterbatch Extruder High Filling Calcium Carbonate Powder Twinscrew Plastic Extruder
This color masterbatch with a high percentage CaCO3 filling extruder could make very good dispersibility and distribution of high filling color masterbatch granules.
HS Code: 8477.2010
Model: SHJ35B, SHJ50B, SHJ52B, SHJ65B,SHJ75B
Output capacity: from 30Kgs/hr to 450Kgs/hr ( according to the various kinds of machine mode.
![]() |
![]() |
Advantage of our twin screw color master-batch & high filling filler master batch extruder machine
1) Good design for color master batch granules making HOST;
2) Good-designed screw segments combination;
3) Special design for feeding barrel and side feeder(optional);
4) Special barrel for color masterbatch granules making;
5) Special design air discharge and vacuum system for color masterbatch granules making;
6) easy and convenient operate controlling power box equipped;
![]() |
![]() |
How to choose a good quality color masterbatch or filler masterbatch extruder machine line?
As you know, good plastic color masterbatch and high-filling plastic pellet products need three effective combinations: proper equipment, good formula, and reliable process, all of which are indispensable. But most of the time, because of the unreasonable formula and the lack of process, users and formula engineers will blame equipment problems. In many cases, after effective communication between the formula engineer and our equipment engineer, the problems encountered will be solved without adjusting the formula and only adjusting the process. Our products pay more attention to the dispersion and distribution of the final plastic color mother to meet the actual needs of users.
Professional knowledge of color master-batch
Master-batch material refers to the process of plastic processing and molding, in order to facilitate the operation, will need a variety of additives, fillers and a small amount of carrier resin for mixing and mixing, the produced granular material is called master material. It’s not clear what the master-batch is for. Why prepare the master-batch? Are there any benefits and convenience in processing?
![]() |
![]() |
Why we use mater-batch?
Master batch is mainly in order to improve the dispersion of some additives, compatibility, improve the environment, to prevent some dust additives flying.
why is there a carrier resin in the master batch?
For example, a flame retardant masterbatch is composed of flame retardant + resin + additives. Why don’t you just take the powdered flame retardant and make it granular and add it to the resin? This kind of process you mentioned exists, but the application is very limited, mainly some additives with a low melting point can do so. It’s very simple to think about, high melting point powder, there’s no resin for bonding, how do you make it granular. A small amount of filler is coated in the polymer matrix to improve the dispersion and compatibility. For example, a flame retardant master-batch is composed of flame retardant + resin + additives.
Why don’t you just take the powdered flame retardant and make it granular and add it to the resin?
The use of master can reduce the dust in the working environment; For the more awkward powder addition amount such as about 5%, the use of masterbatch can not worry about powder particle separation; The final use of master granules is equivalent to a secondary dispersion, which helps to improve the dispersion of the additive
In particular, the additive of the powder layer can avoid the damage of the powder layer after making a master-batch. The base material is also the main raw material for production and use, which will greatly improve the dispersion of subsequent products. There is also the color master, which adds the color powder to the base material to make a high concentration of color master, convenient storage and transportation, and convenient use.
What is the color master-batch?
Color master, also known as color, color master batch, is a new type of polymer material special coloring agent, also known as PigmentPreparation. It is composed of pigment or dye, carrier and additive three basic elements, is the super constant pigment or dye uniformly attached to the resin and obtained aggregate, can be called pigment concentration (PigmentConcentration), so its coloring power is higher than the pigment itself. To put it simply, a masterbatch is an aggregate made by uniformly binding a superlarge amount of pigment or dye to a resin. Master batch technology is very strict, the general use of master batch technology is wet process. Color masterbatch material by water phase grinding, phase transformation, water washing, drying, granulation, only in this way the quality of the product can be guaranteed. In addition, while the pigment is grinding, a series of color masterbatch technology testing should be carried out, such as measuring the fineness of the grinding grout, measuring the diffusion property of the grinding grout, measuring the solid content of the grinding grout and measuring the fineness of the color paste.
How is the color masterbatch processed? How to get the color master-batch?
A mixture of resin and a large amount of pigment (up to 50%) or dye to produce a high concentration of color.
When processing with a small amount of color master and uncolored resin mixed, can reach the design pigment concentration of coloring resin or products.
Its advantages are: no environmental pollution, simple coloring, accurate measurement, easy dispersion and so on.
Applicable resins are polyethylene, polypropylene, polyvinyl chloride and so on.
Processing methods are extrusion, calendering, etc.
Products are pipe, sheet, wire and cable, fiber, artificial leather, film and so on.
Process |
Representative materials |
Mixing nature-changing |
PE,PP,PS+SBS,PA+EPDM,PP+NBR,EVA +Silicon rubber, etc. |
PE,PA,PC,CPE+ABS(alloy),PBT+PET,PP+ PE etc. |
|
Filling nature-changing |
PE,PP,EVA, etc.+ Calcium carbonate, talcum powder, titanic powder ABS,PC,PS, etc.+ aluminum hydroxide, magnesium hydroxide, antimony oxide. |
PP,PA,ABS +ferrous powder, sulphuric powder ceramic powder |
|
Functional machine pellets |
PP,PA,ABS,PBT, etc+ anti-burning agent and other auxiliary agents: combustion-supporting machine pellets |
PE,PP,PS, etc+ starch: de-composing machine pellets |
|
PE+ fog-preventing dipper, stabilizer: dual-prevention machine pellets |
|
PE,EVA=ABS etc+ carbon black: black machine pellets |
|
Colored machine pellets |
PE,PP,ABS,AS,PA,EVA,PET +pigment and auxiliary |
Intensified glass fibers and carbon fibers |
PP,PBT,ABS,AS,PA,PC,POM,PPS,PET etc.+ long fibers, small fibers, carbon fibers, crystals and so on, etc. |
Various cables |
HDPE,LDPE,LLDPE,MDPE,EVA,PVC,PP, etc. insulating cables,coatings, PE peroxide silicon alkyl crossing cables: radialization crossing cables |
Special materials |
EVA heat-melting glue, polyurethane, fluorine rubber, fluorine plastics, PP cigarette filtering material and TPR sole material |
Reaction extruding |
Poly-amide condensate, poly-amide melting polymerization, poly-amide polythene-adding, poly-carbonate condensate, etc. |
Exhausting and volatilization |
Polystyrene oxide, high-absorbing resin, chlorine sulphur polyethylene |
Powder paint |
Polyester, ring oxide, lactide, polyurethane, acrylate |